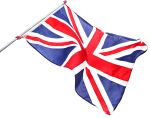
Manufacturing In-House: A Commitment to Quality at Locker Wire Weavers
At Locker Wire Weavers Ltd, we pride ourselves on being a leader in the wire mesh fabrication industry for over 150 years. We specialise in wire mesh and associated components, offering high-quality products that are tailored to meet our customers’ unique needs. In an age where outsourcing is increasingly common, we firmly believe in the advantages of manufacturing in-house. Our dedication to local production not only showcases our expertise but also strengthens our commitment to quality control at every stage of the manufacturing process.
Power Pressing of Mesh Filter Discs
Filters, screens and sieves are often cut and formed from wire mesh sheets. Locker use high-quality power presses and tooling to ensure that each filter disc is cut and shaped with precision and accuracy. Our team of experienced operators meticulously controls every aspect of the pressing process to achieve consistency and reliability.
The capability to manufacture these discs in-house allows us to adhere to strict quality standards whilst providing our customers with quick turnaround times. Each mesh filter disc we produce reflects our pride in craftsmanship and commitment to excellence.
Welding PVC Edging to Metal Mesh Screens: Combining Functionality and Durability
One of our specialised processes is the welding of PVC edging to metal mesh screens. This critical step enhances not only the aesthetic appeal of our products but also their durability and functionality. Eyelets can also be pressed into the PVC edging strips, to facilitate mounting of the mesh screen. Our skilled technicians use advanced welding techniques to seamlessly bond the edges, ensuring a secure and long-lasting finish.
By keeping this process in-house, we can closely monitor quality, ensuring that every screen meets our high standards for performance and visual appeal. The result is a reliable product that stands up to the demands of various applications while enhancing user safety.
Electro Seam-Welding of Large Metal Mesh Sheets
At Locker Wire Weavers Ltd, we have mastered the technique of seam electro-welding, with precise control and regulation of electrical current, allowing us to join large, fine metal mesh sheets with unmatched strength and precision. This process is pivotal when creating larger structures where strength and stability are paramount. Our experienced welders employ state-of-the-art equipment to deliver continuous joints that minimise the risk of failure.
By manufacturing this essential step locally, we maintain strict control over quality and consistency, ensuring that our clients receive products that withstand the test of time.
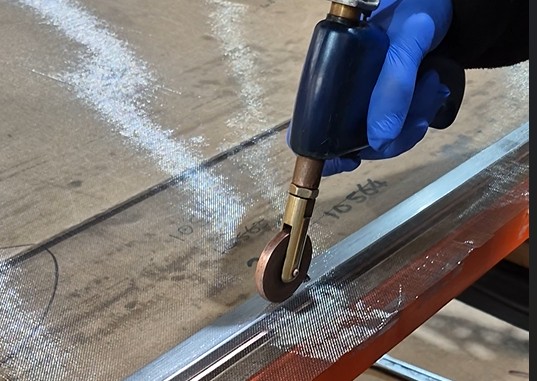
Welding Fine Mesh to Metal Frames Using Low Current Seam Welding
Another key aspect of our in-house manufacturing capabilities is the welding of fine mesh to metal frames using low current seam welding. It is notoriously difficult to weld what can be a very fine gauge metal mesh to a much larger gauge metal frame without burning holes in, or weakening the mesh.
This process is crucial for applications requiring delicate yet dependable structures, such as industrial filters and protective barriers. Our skilled technicians’ expertise in low current techniques ensures minimal material distortion, preserving the integrity of the fine mesh. Maintaining this process within our facility not only guarantees high-quality outcomes but also allows us to innovate continuously, aligning our products with evolving market needs.
Slitting of Large Mesh Rolls into Strips: Tailored Solutions for Customers
An essential part of our operation is the slitting of large mesh rolls into strips to meet our customers’ specific requirements. This capability enables us to provide tailored solutions for our clients, ensuring that they have access to the precise dimensions and quantities they need for their projects. Our precision slitting machines have been developed by us over many years and are operated by skilled personnel who prioritise accuracy and efficiency. By taking this process in-house, we enhance our responsiveness and flexibility, allowing us to serve our customers better and strengthen our relationships.
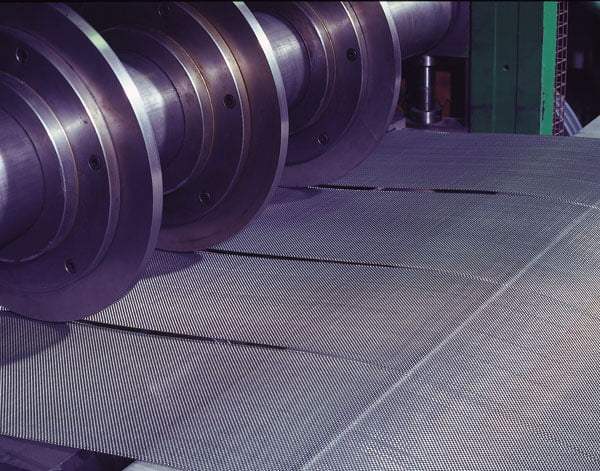
Inspection of the Fine Metal Cloth: Commitment to Quality Control
Quality control is a fundamental aspect of our manufacturing philosophy at Locker Wire Weavers Ltd. Once our fine metal cloth is produced, it undergoes a rigorous inspection process. Our experienced quality control team meticulously examines each roll of mesh, checking for consistency, durability, and adherence to specifications. This unwavering commitment to quality ensures that we deliver products that not only meet but exceed our customers’ expectations. By keeping inspection in-house, we maintain full oversight of our quality assurance processes, allowing us to continuously improve and innovate.
Experience the Difference
At Locker Wire Weavers, our pride in manufacturing in-house stems from our deep-rooted expertise and commitment to quality control. Each process, from power pressing and welding to slitting and inspection, is carried out with the utmost care and attention, reflecting our dedication to excellence. Manufacturing locally not only enhances efficiency and responsiveness but also strengthens our relationships with customers and our community.
As we celebrate over 150 years of service, we remain committed to upholding the highest standards in wire mesh and associated components. We invite you to partner with us and experience the quality and craftsmanship that has made Locker Wire Weavers a trusted name in the industry. Together, we can build solutions that stand the test of time.