Key Benefits of Our Wire Mesh Discs and Filters
- Custom sizes and shapes to meet exacting standards
- Exceptional durability using stainless steel and specialty alloys
- Engineered for critical industries, including filtration and extrusion
- Spotless, accurate punching for superior fit and performance
- Fully supported from design to fabrication
Introduction: When Manufacturing Becomes Mastery
At Locker Wire Weavers Ltd, punching out wire mesh discs and filters is far more than a mechanical operation — it’s a craft honed over 140 years of innovation and excellence. Blending traditional wire weaving knowledge with cutting-edge technology, we deliver bespoke wire mesh components that meet the rigorous demands of modern industrial applications.
Whether you're in polymer filtration, plastic extrusion, process sieving, or hydraulic filtering, our punched mesh discs and filters are built with one goal: performance without compromise.
How Wire Mesh Filters Are Made: Behind the Punch
Wire mesh filters and discs begin their journey as high-spec woven wirecloth, often in stainless steel or specialty alloys like Monel or Inconel. The mesh is then precision-cut into discs, washers, or other complex shapes using:
- High-speed punching presses
- Laser or plasma cutting systems for intricate geometries
- Spot or edge-seam welding for multi-layer mesh discs without edging
- Edge binding with stainless steel, aluminium, or copper
Applications: Engineered for Demanding Environments
Our mesh discs and filters are critical in countless industries:
Filtration & Extrusion
- Spinneret filters for fibre production
- Extruder screens and disc packs for plastic and rubber processing
- Multi-layer screen packs to capture fine contaminants
Gas & Liquid Flow Control
- Diffusers and contact aids in chemical processing
- Inline filters in food, pharma, and petrochemical pipelines
Mechanical and Environmental Use
- Breather vents, vacuum screens, and dust caps
- Spark protection and flame arrestors in hazardous zones
We also provide custom-fabricated filter elements, ready for integration into larger assemblies.
Product Example: Mesh Spinneret Filter
Diameter | 75 mm (customisable) |
---|---|
Layers | 1 (multi-layers & graduated mesh sizes available) |
Material | 316L Stainless Steel + aluminium rim |
Application | Polymer fibre extrusion line |
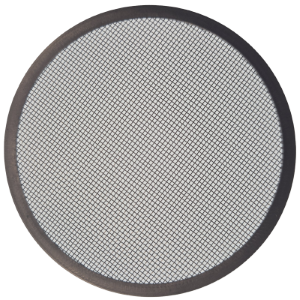
Why Locker? Expertise Forged Over Generations
Founded in 1878, Locker Wire Weavers was a pioneer in wire weaving, reputedly the first to use steam-powered looms for industrial mesh production. Today, we continue to lead in:
- Technical advice and engineering support
- Stockholding of hundreds of mesh specifications
- Fabrication of complete filter assemblies and framed screens
All of our products are made under ISO 9001:2015-certified quality systems, and we are committed to exceeding industry expectations in every aspect of service and delivery.
FAQs: Wire Mesh Discs and Filters
What mesh sizes are available for punched discs?
We stock mesh from 150 mm down to 1 micron nominal. Custom combinations of aperture and wire diameter can be made to spec.
Can Locker provide rimmed or framed mesh filters?
Yes. We offer edge binding in stainless steel, copper, and aluminium. We also fabricate framed mesh panels and multi-layer packs.
What industries do you supply?
Our punched mesh filters are used in:
- Polymer & rubber extrusion
- Food and beverage processing
- Oil & gas
- Pharmaceutical
- Automotive and aerospace
Do you offer design or prototyping help?
Absolutely. Our Warrington-based engineering team provides full consultation, from concept to prototype to production-ready part.